Progressing Cavity Pumps N series
The Diamond N series represents the best solution for the industrial sector in pumping a wide range of fluids. They are synonymous with robustness, reliability, performance, and application flexibility.
Designed according to the most demanding standards, they comply with API 676 regulations.
Suitable for pumping both viscous and non-viscous products, with or without solids of any kind, they are the ideal solution for those seeking a high-tech standard product with an unmatched cost-benefit ratio in the current progressive cavity pump market.
The N series stands out for its pump-to-motor coupling type: DN,JN and FN
Operating ranges

Flow rate

Pressure

Temperature
Applications
Discover the product's application characteristics Progressing Cavity Pumps N series
Models
Size | Model | QMAX 2 BAR [m³/h] | RPM MAX | P MAX [bar] |
---|---|---|---|---|
D020 | 1L1 | 4,9 | 1400 | 6 |
D020 | 05K2 | 2,5 | 1400 | 12 |
D020 | 025K4 | 0,7 | 800 | 24 |
D025 | 2L1 | 10 | 1400 | 6 |
D025 | 1K2 | 5,1 | 1400 | 12 |
05K4 | 05K4 | 1,5 | 800 | 24 |
D025 | 025K8 | 0,7 | 800 | 48 |
D030 | 4L1 | 14 | 1000 | 6 |
D030 | 2K2 | 7,2 | 1000 | 12 |
D030 | 1K4 | 2,9 | 800 | 24 |
D030 | 05K8 | 1,5 | 800 | 48 |
D040 | 10L1 | 22 | 800 | 6 |
D040 | 4K2 | 11,5 | 800 | 12 |
D040 | 2K4 | 4,2 | 600 | 24 |
D040 | 1K8 | 2,4 | 800 | 48 |
D040 | 16L1 | 32,5 | 800 | 6 |
D040 | 8K2 | 16,8 | 800 | 12 |
D040 | 4K2EL | 11,5 | 800 | 18 |
D060 | 20L1 | 39,1 | 700 | 6 |
D060 | 10K2 | 17,2 | 600 | 12 |
D060 | 4K4 | 7,2 | 500 | 24 |
D060 | 2K8 | 4,2 | 600 | 48 |
D060 | 30L1 | 46 | 700 | 6 |
D060 | 16K2 | 21,5 | 600 | 12 |
D060 | 10K2EL | 17,2 | 600 | 18 |
D120 | 40L1 | 65,5 | 600 | 6 |
D120 | 20K2 | 31 | 600 | 12 |
D120 | 10K4 | 11,7 | 400 | 24 |
D120 | 4K8 | 7,3 | 500 | 48 |
D120 | 60L1 | 82 | 500 | 6 |
D120 | 30K2 | 40,5 | 500 | 12 |
D120 | 20K2EL | 31 | 600 | 18 |
D300 | 80L1 | 88 | 400 | 6 |
D300 | 40K2 | 45 | 400 | 12 |
D300 | 20K4 | 21 | 400 | 24 |
D300 | 10K8 | 11,7 | 400 | 48 |
D300 | 120L1 | 120 | 400 | 6 |
D300 | 60K2 | 64,5 | 400 | 12 |
D300 | 40K2EL | 45 | 400 | 18 |
D400 | 160L1 | 161 | 400 | 6 |
D400 | 80K2 | 90 | 400 | 12 |
D400 | 40K4 | 45 | 400 | 24 |
D400 | 20K8 | 19,5 | 350 | 48 |
D400 | 240L1 | 261 | 400 | 6 |
D400 | 120K2 | 116 | 350 | 12 |
D400 | 80K2EL | 90 | 400 | 18 |
D400 | 40K2E | 45 | 400 | 24 |
D400 | 20K4E | 19,5 | 350 | 48 |
D500 | 320L1 | 255 | 350 | 6 |
D500 | 160K2 | 142 | 350 | 12 |
D500 | 80K4 | 56 | 250 | 24 |
D500 | 40K8 | 26 | 250 | 48 |
D500 | 480L1 | 368 | 350 | 6 |
D500 | 240K2 | 185 | 350 | 12 |
D500 | 160K2EL | 142 | 350 | 18 |
D500 | 80K2E | 56 | 250 | 24 |
D500 | 40K4E | 26 | 250 | 48 |
D600 | 640L1 | 540 | 350 | 6 |
D600 | 320K2 | 280 | 350 | 12 |
D600 | 160K4 | 101 | 250 | 24 |
D600 | 80K8 | 51 | 250 | 48 |
D600 | 960L1 | 802 | 350 | 6 |
D600 | 480K2 | 403 | 350 | 12 |
D6 | 320K2EL | 280 | 350 | 18 |
D600 | 160K2E | 142 | 250 | 24 |
D600 | 80K4E | 56 | 250 | 48 |
Materials
Casing materials
Wide selection of cast iron, alloy, and stainless steel bodies, including corrosion-resistant options for harsh environments.
Coatings
On request, solutions such as fluoropolymers and ceramic coatings to ensure superior performance.
Seal Shaft Materials
Steel and special alloy materials with advanced coatings to ensure long durability and resistance, as well as advanced protective coatings such as ceramic oxides and tungsten carbide.
Optional for coupling rod
Joint protection
Coupling rod with feed screw
Anti-settling impeller
Balanced hydraulic joint
(For details, see the brochure constructive options, equipment and installations)
Materials of Rotors
Steel and special alloy materials with advanced coatings to ensure long-lasting durability and resistance.
Materials of Stators
We offer a wide selection of compound materials for stators, designed to ensure high performance and durability in diverse industrial environments.
Among the available options, we can provide elastomers and special materials, including food-grade compounds and high-performance solutions.
These solutions can be customized based on the specific needs of the customer and the operating conditions.
Connections
Flanges and threaded connections for various applications, including food-grade models and high-pressure environments.
Compliant with UNI, DIN, and ASME standards.
Sealing Systems
Various types of mechanical seals, both single and double, cartridge-style; also available with flushing solutions in accordance with API standards.
Bases
- standard Base
- API 676 Base
- Base with anti-vibration housing (feet spacer)
- Base with risers
- Skid with lifting devices
- Cart for industrial sector (trolley)
- Cart for food grade and winery sector
(For details, see the brochure constructive options, equipment and installations)
Optional
Equipment and optional
- Stator heating jacket
- Temeprature probe for dry running protection (standard in the ATEX version)
- Flow switch
- Heating jacket for body pump
- Stainless steel stator cover
- Industrial flanged Bypass (or with threaded connection)
- Quench Pot flushing
- Stainless Steel Lantern
- Hermetic lantern
- Carter to protect the motorization
(For details, see the brochure constructive options, equipment and installations)
Variants
DN series
The motor is directly coupled to the pump by means of a flange. This solution is extremely cost-effective and compact, significantly reducing installation costs and simplifying maintenance. The forces generated by the hydraulic part are supported by the motor. Each motor used has been suitably selected on the basis of restrictive technical parameters and subjected to numerous durability tests under heavy loads. The DN series is the reference point for almost all pumps installed in industry.
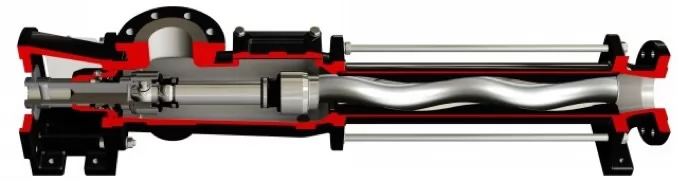
JN Series
The motor is connected to the pump input shaft via coupling. It is the best solution in terms of performance and durability. All the forces generated by the pump are absorbed by the bearings in the support. These bearings have a very high load resistance. They are mounted with extreme precision on components of the highest quality. It is the best solution when you want to ensure maximum durability and reliability, while requiring larger installation spaces. The bearing holder we designed is modular and can be installed later in a pump with DN series block holder. Represents the state of the art in this type of installation.
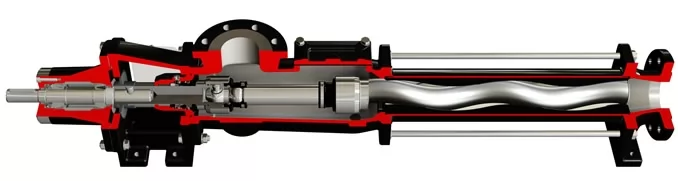
FN Series
The motor is directly coupled to the pump via the flange of the bearing support module.
This solution is the most versatile as it allows the use of standard flanged gearboxes and output shaft, coupling with hydraulic or pneumatic motors, maintaining the simplicity and compactness of the classic monobloc solution while guaranteeing total reversibility and superior bearing support performance.
This bearing support module can be applied to the entire Diamond series and allows for quick maintenance of the motor drive. FN is therefore synonymous with modularity and reliability with any type of motor.
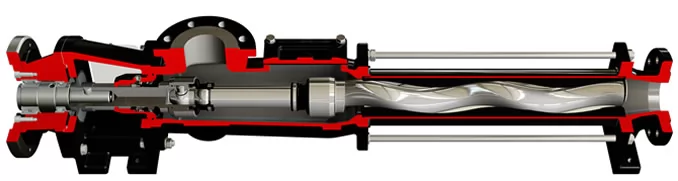
JN Series (API)
JN Series Progressive Cavity Pump – API Variant
The JN series progressive cavity pump in the API variant is specifically designed to meet the demanding requirements of the oil & gas sector. Equipped with a base compliant with API 676 and offering the possibility of mechanical seals according to API 682, this pump ensures high reliability and adherence to industry standards.
The motor is connected to the pump input shaft via a coupling, providing the best solution in terms of performance and durability. All the forces generated by the pump are absorbed by high-load capacity bearings housed in a robust support, designed for maximum precision and quality. This setup ensures exceptional longevity and reliability, making it ideal for demanding applications, albeit requiring larger installation spaces.
Additionally, the modular bearing support we designed can be retrofitted to a DN series block pump, offering versatility and upgradeability. This engineering approach represents the state of the art for this type of installation, ensuring compliance with the highest industry standards
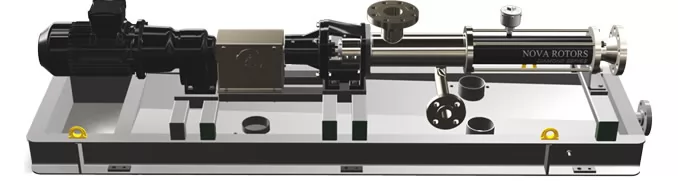
DN series (Inox version)
The motor is directly coupled to the pump by means of a flange. This solution is extremely cost-effective and compact, significantly reducing installation costs and simplifying maintenance. The forces generated by the hydraulic part are supported by the motor. Each motor used has been suitably selected on the basis of restrictive technical parameters and subjected to numerous durability tests under heavy loads. The DN series is the reference point for almost all pumps installed in industry.
This version PCP pump DN stands out for its use of food-grade elastomers, a stainless steel casing, and a stainless steel rotor and transmission. It is suitable for use with food products.
However, for optimal hygiene, we recommend the X series pump, which is specifically designed for sanitary applications. X series is also comply with 3-A sanitary standard and EHEDG
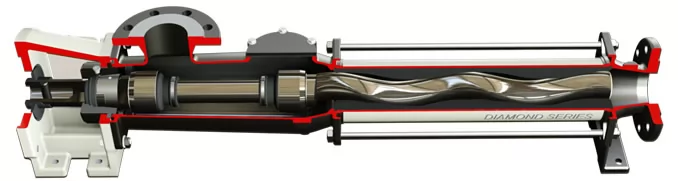
- Extremely robust supports, suitable for sustaining motor loads.
- Rotating parts made of stainless steel as standard, even for cast iron pumps. Various metallurgies available depending on the application.
Different options for the drive shaft depending on requirements. - Large suction sections ensure excellent priming capability and efficient pumping of viscous substances.
The pump body can be made from different metallurgies as needed.
Available connections: UNI EN / DIN or ANSI. - Inspection ports are standard across the entire range for effective cleaning of the pump bodies.
- Discharge sections are designed to minimize pressure losses.
The discharge nozzle can be manufactured in different metallurgies as required.
Available connections: UNI EN / DIN or ANSI. - Abrasion-resistant rotors and stators allow for the pumping of highly viscous fluids with solid particles in suspension.
The rotor can be supplied in various base materials and can be heat-treated or coated to enhance durability.
Stators can be configured with various types of elastomers. - Patented pin joint, the core of the Diamond series pumps.
It combines compactness and ease of maintenance with performance, reliability, and durability without compromise. - Various sealing systems available, including:
Packing with or without flushing, Single mechanical seal with or without quench,Double mechanical seal in back-to-back or tandem configuration. Quench and double seals must be flushed according to API PLAN suitable for the process.
A wide range of seals compliant with ISO EN 12756 can also be installed to meet any application needs. - Connection via pins to the motor or bearing housing.
This is the simplest maintenance solution and allows the pump to operate in reverse rotation.
The splash guard ring protects the motor shaft from corrosion, further facilitating maintenance. - J AND F BEARING SUPPORT Modular J bearing support
High-performance bearings ensuring maximum reliability
The alternative with F support allows for the connection of reducers with standard output shafts while also improving performance.
