Chemical Industry
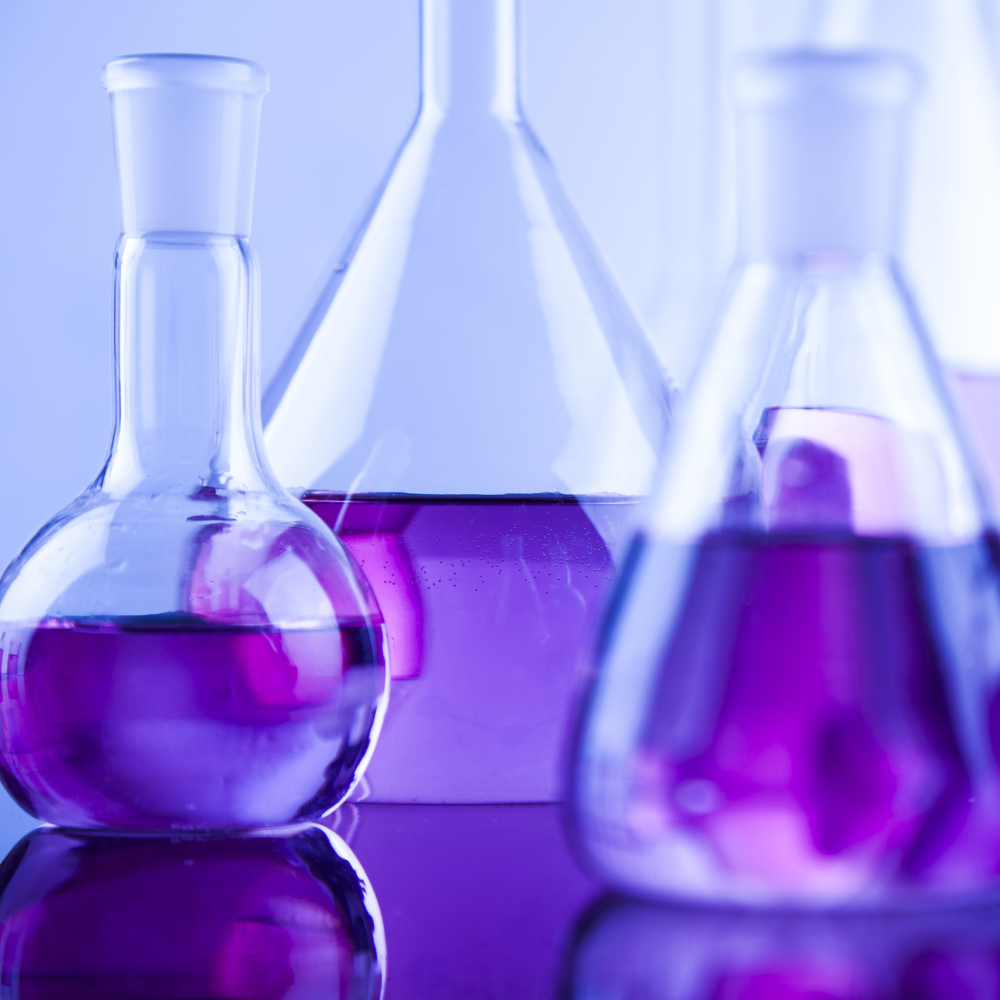
Highly Safe Solutions for Chemical Fluid Pumping
The chemical sector is defined by complex processes that require reliable and durable equipment capable of handling fluids with highly variable properties, such as viscosity, corrosiveness, and the presence of solid particles. Every stage of chemical production and treatment demands precise, efficient, and safe pumping solutions to ensure product quality and compliance with environmental regulations.
Nova Rotors progressive cavity pumps are a benchmark for the chemical industry, thanks to their design that enables the safe and efficient handling of challenging fluids, reducing risks and optimizing operations.
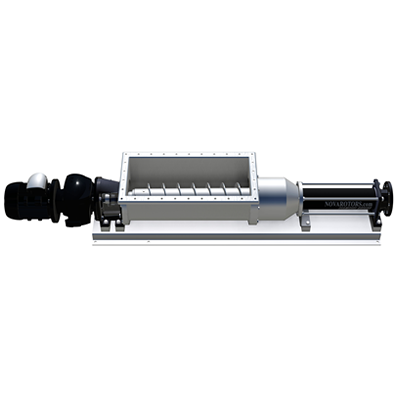
HS Pumps
Hopper Progressive Cavity Pump with Screw Conveyor: Designed for transporting pasty chemical products, high-viscosity sludge, and mixtures with a high solid content.Ideal for transferring resins, abrasive pastes, process sludge, and production waste.
Suitable for disposal and recovery processes of dense or hard-to-handle chemical materials.
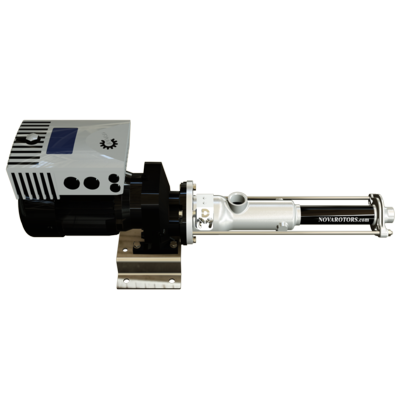
M Pumps
Dosing Progressive Cavity Pump: Perfect for precise dosing of chemical additives, catalysts, and reagents in production processes.
Ideal for controlled injection of polymers, acids, bases, and other substances in treatment systems.
Ensures continuous, pulsation-free dosing, essential for sensitive chemical processes.
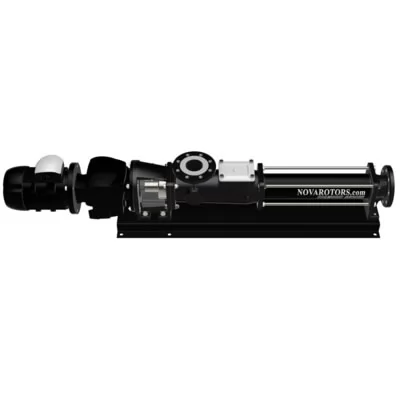
N Pumps
Perfect for transferring sludge from waste treatment and purification processes, including chemical-physical effluents. Also ideal for pumping thickened sludge to centrifuges or screw presses, optimizing dewatering and waste volume reduction.
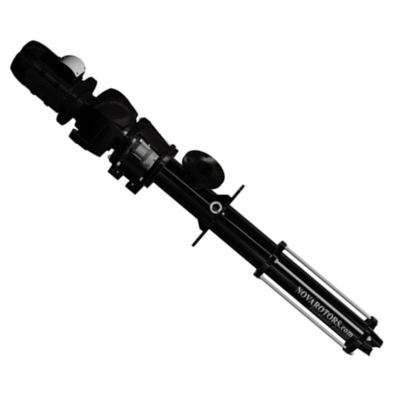
V Pumps
Used for transferring liquid chemicals directly from tanks, drums, or containers.Perfect for safely and efficiently emptying solvents, industrial oils, emulsions, and other chemical products.
Minimizes waste and facilitates fluid dosing and management in industrial environments.
Main Applications
Handling of Aggressive Chemical Fluids
Pumping of acids, bases, and highly corrosive solvents for production processes.
Transfer of Viscous and Abrasive Fluids
Handling of paints, resins, adhesives, and other high-viscosity fluids containing solid particles.
Precise Dosing of Chemical Additives
Ideal pumping solutions for accurate, pulse-free dosing, essential in chemical synthesis processes.
Chemical Waste Treatment
Safe management and disposal of process residues, waste fluids, and hazardous substances, reducing environmental impact.
Applications in Hazardous Environments
Certified pumps for use in explosion-risk areas Atex, such as flammable chemical production plants.
Key Strengths
We stand out for our ability to provide tailored solutions for the chemical industry, offering pumps designed to deliver exceptional performance even in the most demanding operating conditions.
- Resistance to Corrosive and Abrasive Fluids – Made with high-quality materials, such as stainless steel and special alloys, Nova Rotors pumps are ideal for handling aggressive chemicals and complex mixtures.
- Safety and Regulatory Compliance – All pumps meet international standards, including ATEX certification for use in explosion-risk environments.
- Versatility – Suitable for a wide range of applications, from transferring viscous liquids to processing fluids with solid particles or highly volatile substances.
- Efficiency and Reliability – Engineered for continuous operation, minimizing maintenance costs and ensuring maximum performance.
With our reliable and customized solutions, the chemical industry can count on an advanced technological partner.
A Commitment to Efficiency and the Environment
Our team of experts is dedicated to supporting the chemical industry with solutions that combine operational efficiency and environmental responsibility. Our pumps are designed to minimize waste and ecological impact while ensuring the safe and responsible handling of chemical fluids.
With Nova Rotors, chemical industry companies can rely on a trusted partner offering advanced technologies to tackle modern industrial challenges, promoting sustainable and cutting-edge processes.
Recommended products
